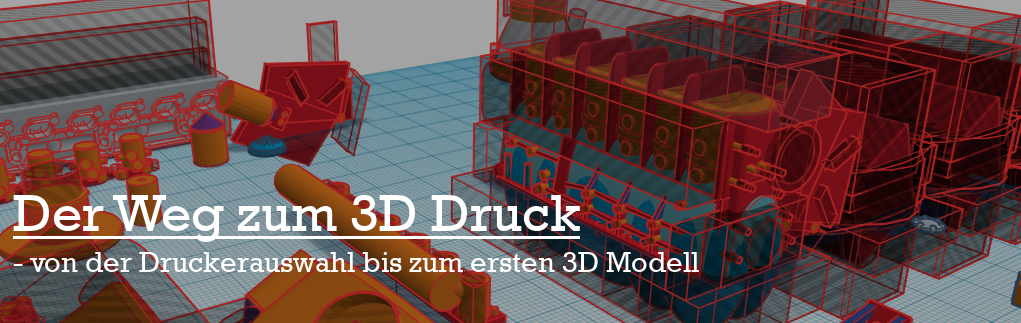
Vorgeschichte
Nachdem ich schon länger elektrische Schaltungen bastelte, stand ich immer wieder vor ein und demselben Problem, irgendwo mussten die Schaltungen nach ihrer Fertigstellung untergebracht werden. So war ich ständig auf der Suche nach passenden Gehäusen. Zum Einsatz kamen bis zu diesem Zeitpunkt meist Abzweigdosen, Fertiggehäuse oder Kunststoffverpackungen (z.B. Ferrero Rocher oder auch Tic Tac). Das Problem dabei war meist, dass diese entweder zu hoch, zu breit, zu lang oder auf irgendeine andere Art nicht genau passend waren. Wollte man in diese Gehäuse dann noch irgendwelche Displays oder Schalter integrieren, war das nur mit dem Einsatz von Bohrmaschine, Schleifbock oder Dremel möglich und das Ergebnis nicht immer wie gewünscht. Aus diesem Grund fing ich Ende 2015 an nach einer Alternative zu suchen und landete recht schnell bei den 3D Druckern.
Der erste Drucker – Prusa I3 Hephestos
Die Auswahl an 3D Druckern war damals zwar schon recht ordentlich, doch da ich weder wusste wie ein 3D Drucker funktioniert, noch wie man die passenden 3D Modelle zum Drucken erstellt, wollte ich natürlich nicht gleich tausende von Euro investieren. Dies war damals aber selbst bei den Einsteigergeräten ein fast schon normaler Preis. Bei meiner Suche stolperte ich dann irgendwann über den Prusa i3 Hephestos* (https://reprap.org/wiki/Prusa_i3_Hephestos/de), ein 3D Drucker ohne Gehäuse, den es damals entweder als Komplettgerät oder Bausatz zu kaufen gab.
Da der Bausatz um einiges günstiger war, bestellte ich mir den Drucker zum Selberbauen nach mehrmonatigem Überlegen und trotz ungläubigem „Kopfschütteln“ meiner Frau, Ende Dezember 2015 für 499.90€ bei Amazon. Die Lieferung erfolgte wie gewohnt innerhalb von 2 Tagen und so nahm ich mir am darauffolgenden Tag Zeit um die gelieferten Einzelteile zu einem funktionsfähigen 3D Drucker zusammenzusetzen. Dies war auf Grund der gut beschriebenen Anleitung kein großes Problem, dauerte aber trotzdem den kompletten Tag, da neben der Mechanik auch die elektrische Verkabelung erledigt werden musste.

[Quelle: https://reprap.org/wiki/Prusa_i3_Hephestos]
Das erste 3D Modell
Als der Drucker einsatzbereit war, ging es ans Erstellen des ersten 3D Modells. Da ich bis zu diesem Zeitpunkt lediglich mit 2D CAD Programmen gearbeitet hatte, suchte ich im Internet nach Softwarelösungen, mit welchen ich für die ersten Druckversuche schnell 3D Modelle erstellen kann. Dabei fand ich mit Tinkercad* (https://www.tinkercad.com/) ein Tool, welches genau diese Anforderung erfüllt. Ohne viel „Drumherum“ kann man durch die Kombination von geometrischen Objekten eigene 3D Teile erstellen. Der Vorteil an Tinkercad* ist, dass es komplett über den Webbrowser zu bedienen ist. Man muss zum Starten keine Software installieren und auch die Konfigurationsmöglichkeiten halten sich in Grenzen. Für einen Anfänger ist Tinkercad* das perfekte Tool, da man damit schnell Erfolge erzielt und druckbare Objekte erhält.
Nach der Bearbeitung des Tinkercad*-Tutorials „designte“ ich mein erstes eigenes Druckteil, einen Schlüsselanhänger mit dem Namen meiner Tochter darauf, welchen meine Frau heute, 5 Jahre später, immer noch an ihrem Schlüsselbund trägt.
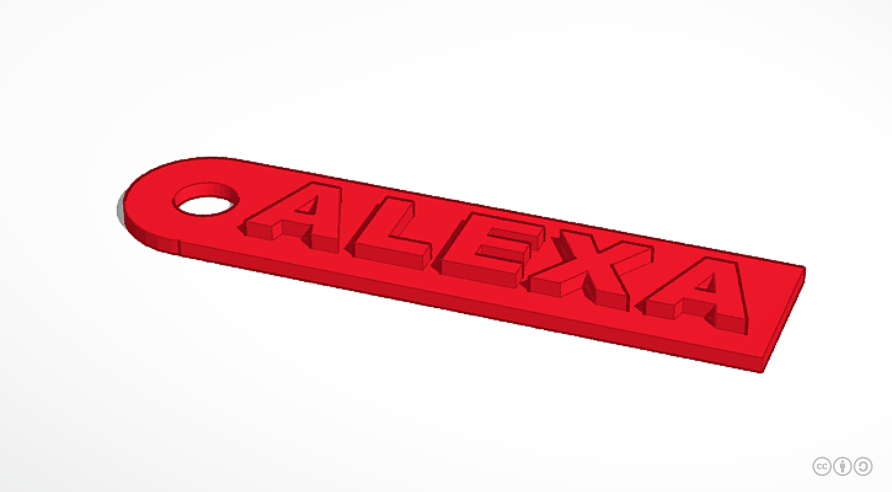
Als der Schlüsselanhänger fertig erstellt und als *.STL-Datei exportiert war, ging es ans Erstellen der vom 3D Drucker verarbeitbaren *.gcode Datei. Diese wird benötigt, da der 3D Drucker mit der *.STL Datei so nichts anfangen kann. Er benötigt vielmehr eine Datei welche ihm sagt, wie er das Objekt Schicht für Schicht aufbauen muss. Dieser Vorgang wird „Slicing“ (abgl. v. engl. slice = Scheibe) genannt. Hierfür verwendete ich die kostenlose Software namens Cura*, welche neben einer unüberschaubaren Fülle an auswählbaren Druckereinstellungen das geladene 3d-Objekt in eben genau diese einzelnen Schichten „zerschneidet“. Für den ersten Druck begnügte ich mich mit den PLA Grundeinstellungen von Cura* (Material, Drucktemperatur, Druckgeschwindigkeit, etc.), da mir die meisten Einstellungen sowieso nichts sagten. Nach dem Speichern erhält man schließlich eine *.gcode Datei, welche dann an den Drucker übergeben werden kann.
Der erste Druck
Nach dem Laden des Filaments navigierte ich im Menü des Druckers zur Objektauswahl und startete den Druck des oben abgebildeten Schlüsselanhängers. Als erstes beginnt der Drucker mit dem Anfahren der Achsen-Endanschläge und dem Aufheizen der Druckdüse bis zur Drucktemperatur. Danach startet der Druckvorgang mit der untersten Schicht des Schlüsselanhängers. Ich war schon ein wenig stolz, dass der selbst zusammengebaute „Haufen“ von Einzelteilen seine Aufgabe auf Anhieb erfüllte und beobachtete gespannt seine Arbeit. Es war faszinierend zu sehen wie ein Objekt, welches gerade noch ausschließlich rein virtuell im Computer existierte, nun in der realen Welt Gestalt annahm. Damit war der Anfang gemacht und ich musste ab dem Zeitpunkt keine Abzweigdosen oder Lebensmittelverpackungen mehr als Gehäuse für meine Schaltungen zweckentfremden, sondern konnte eigene maßangefertigte Gehäuse herstellen.
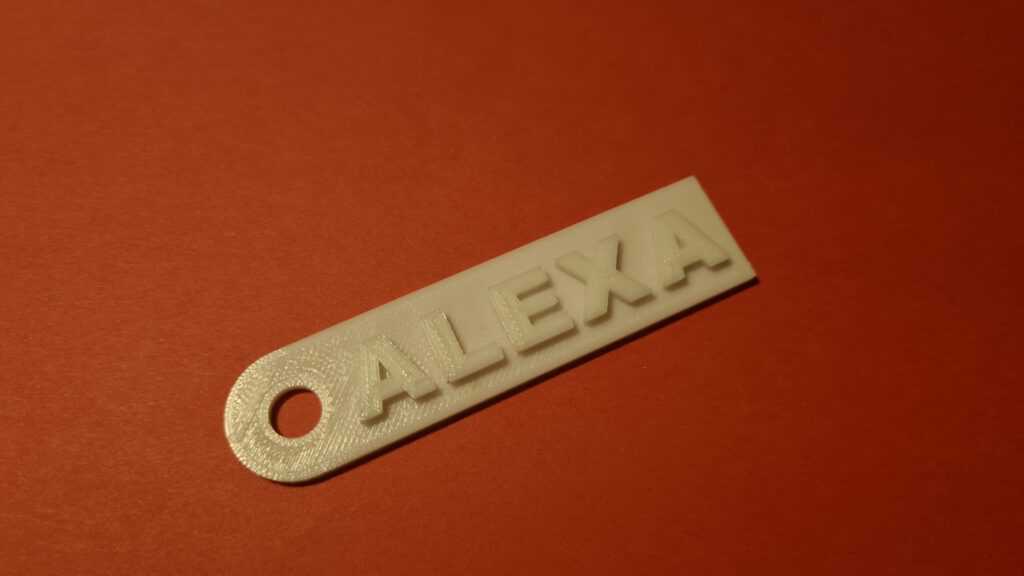
Erste Erfahrungen – PLA und Hitze sind keine gute Kombination
Nach einigen Teilen für den Hausgebrauch hatte ich für meine Arbeit als Prüfstandstechniker in der Motorenentwicklung auch immer wieder Ideen, welche mir die Arbeit erleichtern könnten. So baute ich zum Beispiel einen Halter für einen Steppermotor inkl. Funkmodul, mit dessen Hilfe ich von der Bedienwarte aus ein im Prüfstand stehendes Netzteil „fernsteuern“ konnte. Nach weiteren kleinen Gehäusen, zeichnete und druckte ich eines Tages einen Halter für eine am Versuchsmotor zusätzlich angebrachte Ölleitung, um diese besser befestigen zu können. Als ich das Teil anbrachte und den Motor auf 100°C erhitzte, stellte ich jedoch fest, dass mein Halter nunmehr eher aus Gummi anstatt aus Kunststoff zu bestehen schien. Nach kurzer Recherche war klar: Das verwendete PLA als Druckmaterial hat eine relativ niedrige Temperaturbeständigkeit. Das Material wird bereits ab 60°C – 70°C wieder weich, was bei meinen 100°C Motortemperatur natürlich eher suboptimal war.
Ich recherchierte weiter und fand heraus, dass ein anderes Filament, nämlich ABS, eine Erweichungstemperatur von 110°C bis 125°C besitzt, was für mein Einsatzgebiet ja ausreichend wäre. Leider las man aber auch, dass dieses Material schwieriger zu drucken sei, da es eine höhere Schrumpfung beim Abkühlvorgang ausweist und auf Luftzug oder Temperaturschwankungen mit Verzug, dem sogenannten Warping*, reagiert. Viele Kommentare meinten sogar, dass der Druck mit einem 3D Drucker ohne Gehäuse nicht möglich sei.
Nachrüsten eines Heizbettes für den ABS Druck
Eines hatten alle Forenbeiträge gemeinsam. Es wurde zwingend ein beheiztes Druckbett empfohlen, womit die erste Schicht des ABS-Drucks besser auf dem Druckbett haften und sich nicht ablösen soll. Außerdem wurde die Verwendung von haftungsverstärkenden Materialien wie Klebstoff, Haarspray, Blue-Tape* oder in Aceton aufgelöstes ABS empfohlen, da diese die Haftung des Druckobjektes ebenfalls erhöhen sollten. Ich bestellte also ein beheizbares Druckbett*, einen Thermistor* zur Temperaturerfassung und entschied mich bei den Hilfsmitteln für das Blue-Tape*, da dies im Umgang den unproblematischsten Eindruck machte.
Nachdem die zum Umbau benötigten Teile inkl. einer Rolle ABS-Filament geliefert wurden, baute ich den 3D Drucker anhand einer Anleitung wie dieser hier* (https://selbstgedruckt.de/heizbett-anschliessen/) auf das beheizte Druckbett um. Für den elektrischen Anschluss nutzte ich zusätzlich ein KFZ-Lastrelais welches ich mit dem Steuerstromkreis an den Ramps und dem Arbeitsstromkreis am Heizbett angeschlossen habe, da der Strom welcher vom Heizbett benötigt wird beim ersten Test ohne Relais zu einer spürbaren Erwärmung der Anschlussklemmen geführt hatte. Außerdem hatte ich den Eindruck, dass das Erhitzen des Druckbettes mit dem „Umweg“ über das Relais spürbar schneller ging.
So ausgerüstet startete ich meinen ersten ABS-Druck. Das Ergebnis war ernüchternd. Solang ich flache Objekte druckte, war alles in Ordnung, doch sobald diese etwas höher wurden, bekam ich Probleme mit Warping und teilweise sogar Ablösungen oder Verformungen zwischen den einzelnen Ebenen. Dieses Problem konnte ich bis zuletzt leider nicht zufriedenstellend lösen.
Fazit
Der Prusa i3 Hephestos* hat mich in die Welt des 3D Drucks eingeführt und mir bis vor einigen Wochen stets gute Dienste geleistet. Die Drucke mit PLA waren von der Qualität her super, zumindest wenn man sich bei der Grundeinstellung des Druckbettes die nötige Zeit genommen hat und in Cura* die richtigen Einstellungen gesetzt waren. Nun hat er Konkurrenz von einem Drucker mit geschlossenem Gehäuse bekommen, welcher von der Handhabung noch einen Ticken komfortabler ist. Der I3 Hephestos bleibt mir trotzdem erhalten, auch wenn er zukünftig wahrscheinlich nicht mehr so häufig zum Einsatz kommen wird.